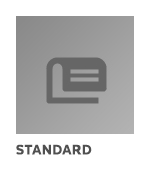
TAPPI T 702 om-22
- Comments Off on TAPPI T 702 om-22
- TAPPI
1.1 In extrusion coating a thin molten polymer film is coated on some kind of substrate. At high extrusion coating speed, even a minor disturbance on the melt web causes major quality problems, which very rapidly lead to large quantities of waste. Therefore, higher coating speeds require polymers with high and even quality in order to avoid waste due to polymer edge instability and web break.
1.2 The rheology-related phenomena that may cause problems in extrusion coating are neck-in (NI) and draw-down (DD). The neck-in is the reduction of the film width and may cause uncoated areas on the substrate. The neck-in is less if the melt elasticity is high. The draw-down is the ability of the melt to be drawn to thin films without breaking. Draw-down is favored by a melt that is more viscous than elastic.
1.3 Changes in the molecular structure have a great impact on the rheological and processing properties of a polymer. Storage modulus and zero shear viscosity have been found to be useful parameters to predict the extrusion coating performance of LDPE. Storage modulus quantifies a material’s ability to store energy elastically and so to deform under stress. As the storage modulus increases, the ability of the material to deform decreases. Zero shear viscosity is related to molecular weight; a small change in molecular weight results in a big change of zero shear viscosity. Knowing this, there is a relation between storage modulus, zero shear viscosity, draw down and neck-in. As storage modulus and zero shear viscosity increase, neck-in decreases and so does the draw down capacity, meaning a lower line speed at which the polymer can be drawn down to a desired thickness.
Product Details
- Published:
- 01/01/2022
- ANSI:
- ANSI Approved
- Number of Pages:
- 4
- File Size:
- 1 file , 330 KB
- Note:
- This product is unavailable in Ukraine, Russia, Belarus